パーツの確認を終え、制作方針がまとまってきたところで手を動かしていくことにします。
まずは制作前の準備から。
制作前の準備
まずは兎に角にもクリアーパーツの保護。
特にクリアーパーツは傷やヒビが入ってしまうと修正が難しいので、別に用意した袋に入れて他のパーツとは分けて保管しておくことにしました。

あとはスキャナーを使ったデカールのデータ化。
万が一失敗した時の備えとしてデータ化しておきますが、それと共に今回はこのデータを使って塗り分け用のマスキングシールを追加で自作する予定でもあるのです。
仮組みの目的と方法

そうしたら次にパーツを切り出して仮組み。
ここでどのように組み立てていくのか、組立てで難しいところは無いか、どのように塗装していけば効率が良いか、強度は十分か、目立つところ・目立たないところはどこか、といったところを確認していきます。
ところで、プラモは作っている対象の特徴が机の上で確認できるのが面白いところ。
上の画像からは前述のモノコック構造が見えてきました。
特にバイクのプラモデルは構造が詳細に再現されていることが多いことから、組立てと同時にバイクの構造や特徴も楽しめます。
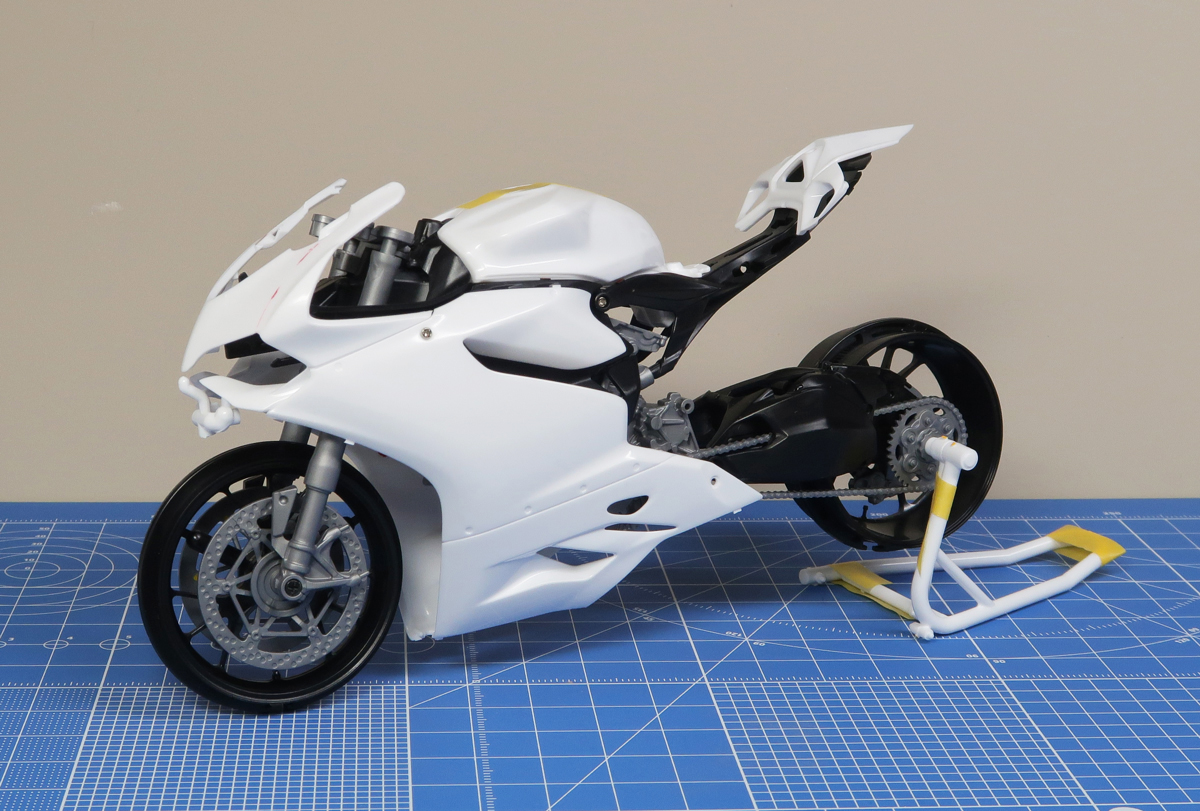
カウルまで取り付けると、バイクの形になってきます。
マスキングテープこそ使っていますが、実はここまで接着剤の類は使っていません。
これはねじ止めの恩恵だったりします。
接着剤を使うと仮組み後の分解に神経を使ったりしますが、ねじ止めであれば外すのも簡単。
仮組みが容易になるのは助かります、有難いです。
ディスプレイケースの制作とバイクの固定方法


ケースへの固定、ディスプレイ方法はこんな感じにしてみました。
基本的には前作の900MHRと同様ですが、多少改良を施しています。

タイヤを支えている透明のパーツは、バイクをより強固に固定するため自作(データ作成→3Dプリント)したもの。
前回作ったパーツは大きすぎて悪目立ちしていると感じていたので、今回は最低限の大きさになるよう調整してみました。
あとレーシングスタンドも活かせるように位置を変更しています。


サイズはこのような感じなのですが、ここで注意が必要なのが赤丸で囲った寸法。
ここにタイヤが挟まるわけなのですが、すかすかだとすぐに外れて意味が無いし、きつ過ぎるとタイヤが入らない。
また、クリアーパーツとして仕上げる予定でもあり、そうすると透明度を上げるために研ぎ出しも必要です。
研ぎ出し=削ることになるので、そこでも寸法は変化します。
(プリンターの種類や素材にもよるが、3Dプリントパーツはクリアー素材であっても透明度が低いものがある)
ということで、赤丸で囲った寸法は削り代を多めにとり(実際に計測した値より1mm程度減らした)、出力後もパーツに実際にタイヤをはめたり外したりしながら削って微調整していきました。
あと、丸穴はネジを通すための穴。
力がかかるパーツにはなるべく接着剤は使いたくなかったため、ねじでケースに固定出来るように予め穴を開けておきました。

こちらはカウルを固定するためのスタンド。
前回同様エンジンも観賞できるようにカウルを外すことにしますが、外したカウルも活かせるようスタンドでケースに固定させます。
ただ、前回作ったスタンドは手間がかかり過ぎた(もうやりたくない)ので、今回はもう少し簡単なものにしてみました。
「簡単な」とはいっても今作はキットそのものの構造を生かしているので、ねじで取り外しも可能。(前作は接着剤で固定)
これにより仮組み・レイアウトの検討・メンテナンスも容易になりました。

参考:前回作ったスタンド(900MHR)

それぞれのスタンドのサイズはこんな感じ。
高さはバイクに装着されたときとあまり変わらない角度になるよう、またケースに固定したときの見栄え等を考慮して設定しています。
キット付属のマスキングシートの活用と、カッティングマシンを使用したマスキングシートの自作

次にキット付属のマスキングシート。
こちらは前述したようにカウルの塗り分け時に絶大なる威力を発揮するアイテムではあるのですが、残念ながら切り抜きがされていません。
そのため、使用時は自分でカットする必要が出てくるのですが、カットラインがけっこう複雑で意外に難易度が高かったりします。
ということで、ここではデジタルを駆使することにしてみました。

使用したのはカッティングマシン。
これは自分で作ったデータをカッターで切り抜いてくれるツールで、デジタルならでは正確性があります。
一言でカッティングマシンといっても家庭用・業務用、対応メディアの大小等で様々な機種があるのですが、一般的なプラモに活用するのであればそんなに大きな機種は必要ないかも。
私は汎用性の高いsilhouette CAMEO4(シルエットカメオ4)を愛用しています。
詳しい操作方法を説明するとなると非常に長くなってしまうのでここでは割愛しますが、簡単な流れはこんな感じ。
①キット付属のマスキングシートをスキャナーでデータ化
②カッティングマシン付属のソフトウェアで、スキャンしたデータをトレースしてカットラインデータを作製
③別に用意したマスキングシートをカッティングマシンにセットしてカット
(キット付属のマスキングシートをカットすることも出来なくないが、位置合わせが面倒くさい)
と、工程自体はけっこう単純。
この方法のメリットは正確性に加えてデータさえあれば同じものを複数作ることができる点。
例え塗装時の塗り分けに失敗したとしても、リカバリーが容易になります。
あとは・・・
カウルの塗り分けにデカールを使うところもあるのですが、デカール貼付の難易度や後々の工程を考慮するとデカールの使用は最小限に抑えたい。
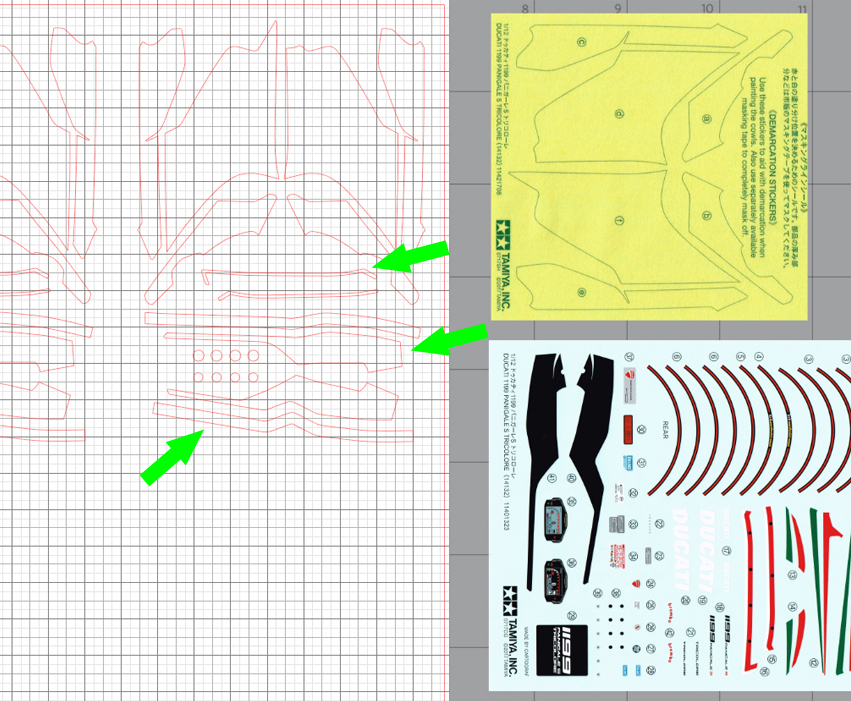
ということで一部のデカールは塗装で対応出来るように、データを利用してマスキングシートを自作してみました。
カッティングマシンを使うとこんな応用技も使えるようになったりします。
https://mobile.twitter.com/ns_factory_100
↓ポチって(クリック)いただけると励みになるので、お願いします!
コメントを残す